In-Depth Analysis of Manufacturing Execution Systems
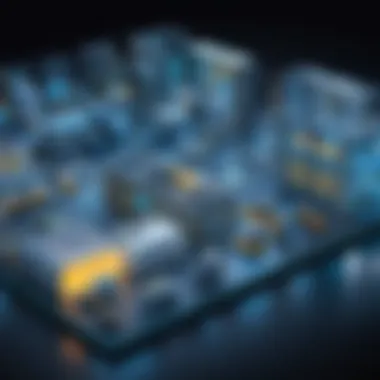
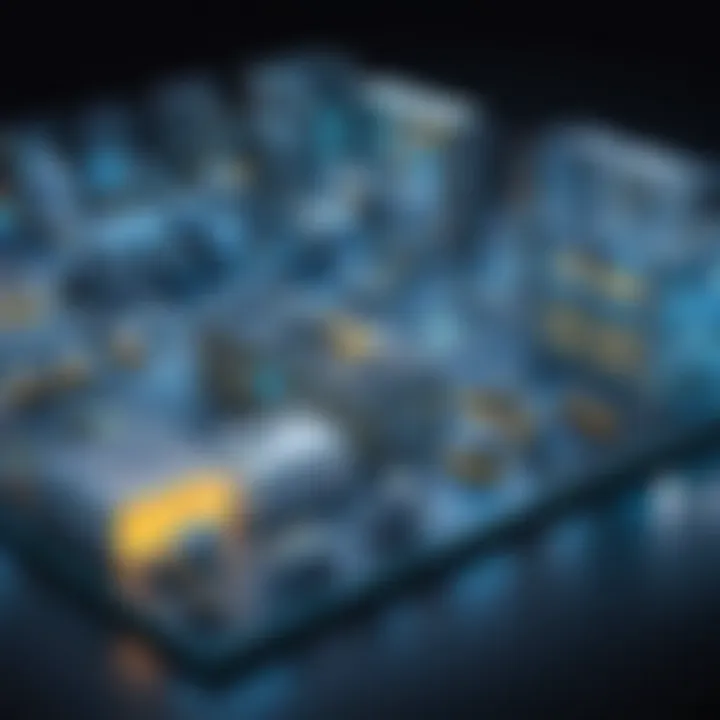
Intro
In the ever-evolving world of manufacturing, adroit management of operations is paramount. Manufacturing Execution Systems (MES) have emerged as frontline solutions to navigate this intricate landscape. These systems act as crucial intermediaries, linking enterprise-level systems with shop floor operations, ensuring real-time data availability and improved decision-making. With more businesses striving for greater productivity and efficiency, understanding MES is not just a technical requirement but a fundamental necessity for professionals within the field.
As we delve into the intricacies of MES, we will explore its architecture, key functionalities, and the many benefits it provides to diverse manufacturing environments. This article touches on the underlying challenges of implementation and unpacks strategies that can help firms leverage MES effectively. Readers can expect a thorough discussion that arms them with the necessary insights to enhance operational processes and stay ahead in a competitive marketplace.
Software Overview
Software Description
At its core, an MES software serves as a bridge between various levels of manufacturing. It integrates processes, resources, and information to ensure that operations are executed efficiently. An MES captures detailed data regarding production schedules, equipment status, and inventory levels. By centralizing this information, it allows managers to make better informed decisions—frequently in real-time. The software can vary significantly in features, complexity, and scope, catering to highly specialized industries as well as general manufacturing processes.
Key Features
The effectiveness of an MES lies in its array of features designed to promote better oversight and control:
- Real-Time Monitoring: Track production processes as they happen, with live updates on equipment and workflow.
- Data Collection: Gather granular data from machines and labor, enabling better analysis and reporting.
- Scheduling and Planning: Optimize the scheduling of production runs based on current resources and capacity, enhancing efficiency.
- Quality Management: Maintain high-quality standards through tracking materials and processes, helping in compliance with industry regulations.
- Integration with Other Systems: Seamlessly connect with ERP systems, reducing data silos and increasing operational synergy.
Through these features, MES systems empower manufacturers to fine-tune their processes and enhance productivity. But all that glitters is not gold. Implementing these systems, while beneficial, does come with its own set of challenges.
User Experience
User Interface and Design
A user-friendly interface is pivotal in ensuring that the MES can be utilized effectively. Engineers and operators should not be bogged down by a complex interface that requires extensive training. A clean layout with intuitive navigation is vital. Some common design principles include:
- Simplicity: Reducing clutter helps users focus on critical tasks without distraction.
- Customization: Allowing users to tailor their dashboards according to their specific needs makes the system more accessible.
- Responsive Design: With the rise of mobile devices, having an interface that works well on tablets and smartphones is increasingly important.
Performance and Reliability
For MES to function optimally, it must exhibit robust performance and reliability. Any downtime can have substantial repercussions. Key aspects to consider include:
- Scalability: As businesses grow, their MES should accommodate increased production demands without compromising performance.
- Security: Protecting sensitive data is crucial; thus, modern MES should have secure protocols in place.
- Support Services: Reliable customer support ensures that any issues can be resolved quickly, minimizing disruptions.
"The right MES can turn data into intelligence, making everyday decisions sharper and fundamentally transforming operational dynamics."
Understanding MES Information Systems
Manufacturing Execution Systems (MES) represent a critical connector in the industrial chain, bridging the gap between enterprise resource planning (ERP) software and the actual production floor operations. Articulating the significance of these systems lays the groundwork for a deeper understanding of their functionalities and contributions. For professionals who are navigating the landscape of modern manufacturing, grasping this connection can yield immense benefits in process efficiency and productivity.
Definition and Purpose of MES
At its core, a Manufacturing Execution System is designed to manage and monitor work-in-progress on a factory floor. It's more than just a piece of software; it's a system that oversees all production activities, ensuring that the right products are made at the right time, under optimal conditions. The purpose of MES can be distilled into several key points:
- Real-time Visibility: MES offers a window into production operations, allowing managers to track all stages of the manufacturing process as they happen. This immediacy contributes to quicker decision-making and enhanced responsiveness to issues.
- Operational Control: The functionalities embedded within MES allow factory managers to control production processes, allocate resources, and uphold schedules efficiently. Control translates to less downtime and maximized throughput.
- Data Management: By gathering and analyzing data from the production floor, MES enables manufacturers to make informed decisions, foster continuous improvement, and enhance overall quality. The need for accurate data cannot be overstated—it informs everything from machine maintenance to customer demand forecasting.
- Integration with Other Systems: An effective MES is not an isolated system. It connects with existing ERP, customer relationship management (CRM), and supply chain management systems. This interconnectedness ensures that information flows seamlessly across all levels of the organization, promoting synergy and enhanced productivity.
In summary, the MES epitomizes the shift towards sophisticated manufacturing environments where data and operational efficiency reign supreme.
Historical Context of MES Development
To appreciate the present significance of MES, it’s essential to glance at its roots. The landscape of manufacturing has transformed remarkably, influenced by technological advancements and changing market demands. Early industrial practices were characterized by simple processes with manual oversight, resulting in fragmented operations and inconsistent product quality.
The 1980s marked a transformative era, emerging with the rise of computer technologies. As manufacturing processes began to integrate digital solutions, the need for a system that could unify diverse operations became evident. The development of MES emerged as a result of this need, motivated by the desire to enhance productivity and reduce waste. Consequentially, the following factors catalyzed its evolution:
- Emergence of Automation: As manufacturing grew more automated, the need for real-time information became apparent. MES was developed to facilitate the collection and management of data from automated machinery, providing factory managers with insights invaluable for operational control.
- Focus on Quality: The push for better quality assurance practices in manufacturing led to the integration of elements for quality control within MES frameworks. This focus has cemented MES as an essential tool in maintaining product standards.
- Need for Integration: The advancement of ERP systems highlighted a gap—there was a need for complementary systems that could enhance the implementation of ERP strategies on the shop floor. MES filled that void, allowing businesses to synchronize overall production management more effectively.
Today, MES continues to evolve, incorporating elements such as IoT and advanced analytics, reflecting its dynamic nature within the rapidly changing manufacturing landscape. The historical context underpinning the development of MES underscores its importance as an integral component of modern manufacturing strategy.
Key Components of MES
Understanding the key components of Manufacturing Execution Systems (MES) is critical for professionals aiming to optimize manufacturing processes. These components are the building blocks that provide vital functionality, ensuring that operations run smoothly from the shop floor to the top management. By integrating these distinct elements effectively, manufacturers can achieve increased productivity, reduced errors, and enhanced visibility throughout the production process.
Data Collection Interfaces
One of the primary features of any MES is its data collection interfaces. These interfaces are responsible for gathering relevant information from various sources across the manufacturing process. Whether it's monitoring machine performance, tracking inventory levels, or logging production times, the ability to collect data in real-time is paramount. This ensures decisions are made based on accurate and timely information, rather than guesswork.
In recent times, manufacturers often employ sensors, barcodes, and RFID technology to streamline data collection. This automated approach minimizes human error and ensures that data is consistently available for analysis. As a result, companies can easily identify trends and anomalies that may impact production efficiency.
"The more accurate your data, the more strategic your decisions can be."
Production Management
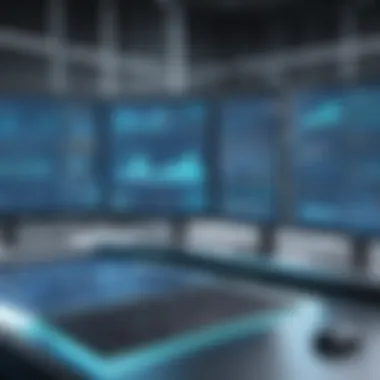
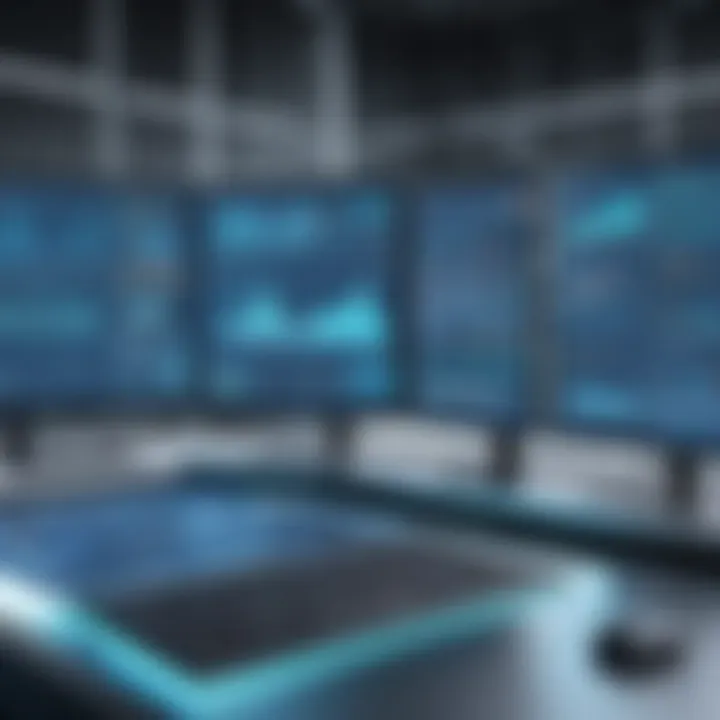
Production management within MES plays a fundamental role in overseeing the entire production lifecycle. This module focuses on scheduling, monitoring, and controlling production processes. It doesn’t stop at merely ensuring products are made; it also looks to optimize the use of resources, manage labor, and ensure schedules are adhered to.
Effective production management can lead to just-in-time manufacturing practices, where products are created as needed rather than in excess. This approach helps to minimize waste and can lead to significant cost savings. Moreover, a robust production management component provides visibility into each stage of production, which can help in identifying bottlenecks that may cause delays.
Quality Control Features
Quality control is another key component of MES that cannot be overlooked. With increasingly competitive markets, delivering products that meet customer expectations is more crucial than ever. Therefore, MES must incorporate stringent quality control measures to track compliance with established standards, assure product reliability, and enhance customer satisfaction.
Tools such as automated inspection processes and built-in reporting systems allow for immediate feedback on product quality. Problems can be addressed as they arise, rather than after the fact, thus reducing the costs associated with rework and defects. A culture of quality can develop when everyone on the production team understands the importance of these features.
Reporting and Analytics
Last but not least, the reporting and analytics capabilities of an MES are indispensable for decision-making. These components allow users to analyze vast amounts of data collected during manufacturing. Reporting functions can produce essential insights into operational efficiency, labor performance, and production timelines.
Companies can generally generate visual dashboards to display KPIs (Key Performance Indicators) and to identify areas needing improvement. With this automated data analysis, manufacturers can make informed decisions quickly, pivoting as needed in response to market demands or operational challenges.
Through effective use of reporting and analytics, businesses can create a culture around continual improvement, harnessing insights to propel better processes.
Benefits of Implementing MES
Understanding the benefits of implementing Manufacturing Execution Systems (MES) is critical for businesses aiming to thrive in today's complex manufacturing environment. Not just a technological upgrade, an MES can radically transform operations at several levels. We explore the significant advantages of MES in enhancing efficiencies, ensuring quality, and managing costs. It's not just about putting in a new tool; it's about optimizing a whole ecosystem.
Real-Time Monitoring
At the heart of MES is real-time monitoring of production processes. Imagine having a surveillance system that tracks every machine, every employee, and every step of the manufacturing line. This continuous flow of data creates a window into operations previously thought impossible. With real-time insights, managers can identify bottlenecks and inefficiencies quickly. How often have you heard stories of delays caused by machine breakdowns or supply chain hiccups? With a real-time system, issues can be addressed before they escalate.
For example, if a machine’s performance dips, the MES can alert operators to investigate right away. A timely intervention can mean the difference between a minor hiccup and a production halt. Moreover, it provides historical data that helps forecast potential disruptions, allowing for proactive adjustments.
"Real-time data is not just a luxury; it's a necessity in today’s fast-paced manufacturing world."
Improved Efficiency
Improved efficiency is another crucial benefit of MES. By automating routine tasks and collating data from various points, MES enables smoother workflows. Consider a factory floor where employees sift through paper logs or spreadsheets to keep track of progress. An MES can cut through the clutter, offering a streamlined process where data flows freely.
This increased efficiency translates to better use of resources—material, time, and human labor. Production rates often increase significantly when waste is minimized and processes are optimized. It’s not uncommon for companies to witness a 10% to 20% uptick in productivity after deploying an MES. That's a staggering impact on the bottom line and operational agility.
Enhanced Quality Assurance
Quality assurance is another area where MES shines brightly. One of the precepts of modern manufacturing is that quality must be built into the process rather than inspected at the end. MES supports this by providing tools for monitoring quality at every stage of production. Through statistical process control, operators can detect defects early, significantly reducing scrap rates.
Imagine a scenario where inspection occurs only at final assembly. With any luck, defects might surface there, but there’s a sizable chance that faulty parts could end up wasting precious materials and time. An MES mitigates this risk by continuously checking standards. Flags trigger when deviations occur, allowing teams to maintain the tight quality control needed in competitive markets.
Cost Reduction Strategies
Finally, let’s talk about cost reductions. Investing in an MES might seem daunting at first glance, but the long-term financial benefits can be substantial. It allows for better resource management, which directly impacts costs. By fine-tuning processes and eliminating waste, companies can lower operational expenses.
Moreover, labor costs can decrease when employees aren’t caught up dealing with inefficiencies. Think about it: a well-implemented MES can keep teams focused on adding value rather than running in circles. To sum it up, the cost savings paired with the uptick in productivity often means that the return on investment can be realized quicker than expected.
Challenges in MES Implementation
Implementing Manufacturing Execution Systems (MES) can seem like climbing a mountain. While the end goal is often a streamlined production process, the path is fraught with bumps and unforeseen detours. The importance of recognizing the challenges in MES implementation cannot be overstated. For IT professionals and businesses alike, knowing these hurdles can pave the way for smoother transitions and better long-term outcomes.
Integration with Existing Systems
Organizations typically have a variety of existing systems in place, from ERP software to various shop floor controls. Integrating MES with these systems can prove to be quite the conundrum. Not only must data compatibility be ensured, but workflows often need to be re-evaluated. This integration requires careful planning and execution.
There are a few key considerations:
- Data Consistency: Different systems may use varying formats or standards, leading to inconsistencies. Making sure that data flows smoothly between MES and existing systems helps in maintaining seamless operations.
- Real-Time Access: If the current systems are not designed for real-time data access, this may hamper the intended functionalities of MES.
- Training Needs: Employees must be trained to understand new integrations, which often involves a period of adjustment.
Resistance to Change within Organizations
Change is rarely welcomed with open arms. Employees may feel comfortable with existing workflows, leading to significant resistance when a new MES is introduced. Such resistance can become a snare if not actively managed. Key factors to consider include:
- Communication: Keeping lines of communication open can help address concerns before they become obstacles. Clear explanations of why the change is necessary can enlist support from employees.
- Involvement: Allowing employees to contribute to the process often lessens resistance. When they see their input valued, they may be more inclined to adapt.
- Staggered Implementation: Instead of a complete overhaul, consider a phased approach. This can make the transition feel less jarring.
Data Security Concerns
In an age where data breaches are all too common, security remains a pressing concern with MES implementation. Protecting sensitive information during and after the installation process is paramount. Potential issues include:
- Access Control: Ensuring only authorized personnel have access to certain aspects of the MES will help maintain data integrity.
- Compliance Risks: Depending on the manufacturing sector, various regulations may apply. Understanding these may require consultation with legal professionals.
- Cyber Threats: With increased connectivity comes increased risk. Assess how external threats could impact your data and implement robust security measures accordingly.
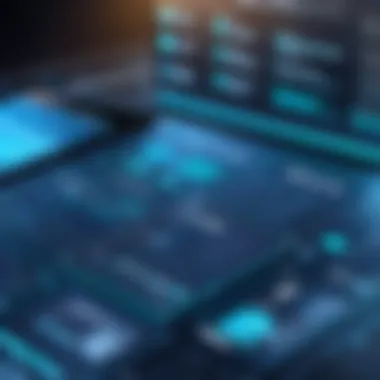
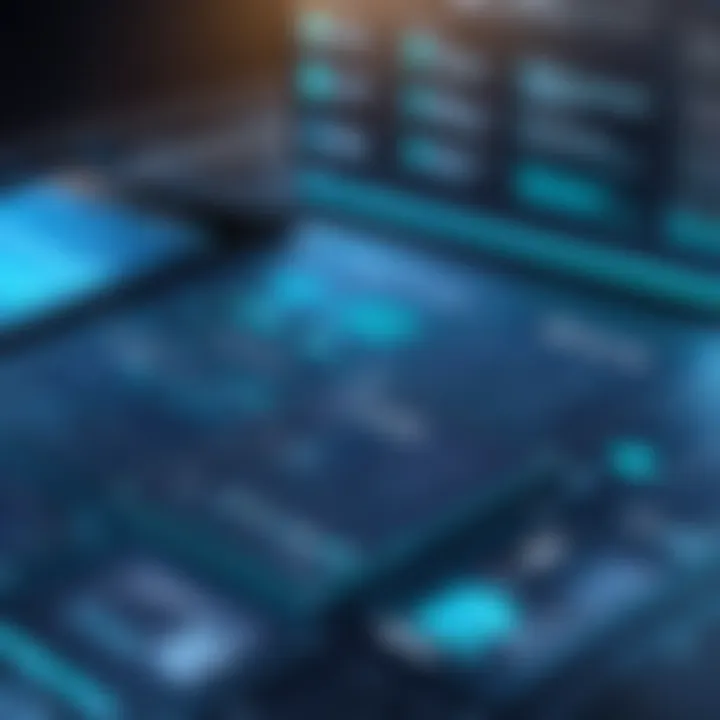
Cost of Implementation
Finally, the cost of implementing MES can often give organizations pause. Initial expenses can sound daunting and may lead to pushback when justifying investments. A closer look reveals few critical components that help put costs into perspective:
- Software Costs: This includes the purchase of the MES software itself, which can vary significantly in price based on complexity and scalability.
- Hardware Upgrades: Older systems may require hardware upgrades for optimal performance, adding to initial expenses.
- Training Costs: Employees require training to use the new system effectively. This should not be glossed over, as it impacts productivity during the transition.
- Long-Term Savings: While the initial outlay may be substantial, the efficiencies gained often lead to long-term cost reductions. It’s vital to calculate potential ROI before dismissing the investment outright.
Adoption of an MES often balances immediate costs against longer-term benefits. Recognizing this can shift the narrative from a burden to a strategic investment.
MES and Industry 4.
The emergence of Industry 4.0 marks a significant shift in manufacturing paradigms, emphasizing increased connectivity, intelligence, and automation. Among the forefront technologies fueling this evolution is the Manufacturing Execution System (MES). MES bridges the gap between enterprise resource planning (ERP) and the shop floor, providing real-time insights that facilitate decision-making and optimize production processes. A seamless integration of MES with Industry 4.0 leads to a more responsive, flexible manufacturing landscape, where data drives innovation.
The Role of IoT in MES
The Internet of Things (IoT) plays a vital role in enhancing MES capabilities. At its core, IoT connects devices and machines, allowing them to communicate and share data effortlessly. In a manufacturing context, this means that equipment on the production line can relay performance metrics, status updates, and alerts directly to the MES. By leveraging IoT technologies, manufacturers gain the ability to:
- Monitor machinery in real-time, catching potential failures before they escalate.
- Optimize resource allocation, ensuring that the right materials and personnel are available when needed.
- Increase productivity by analyzing data to identify bottlenecks and inefficiencies.
Through these enhancements, manufacturers are better positioned to adapt quickly to changing demands and streamline their operations, making IoT a cornerstone of modern MES implementations.
Data Analytics and Machine Learning Integration
As manufacturers collect vast amounts of data through MES, the integration of analytics and machine learning becomes imperative. Data analytics helps organizations interpret the raw data generated by machines, while machine learning algorithms learn from this data over time, identifying patterns and trends that might not be visible to the human eye. The benefits of this integration are profound:
- Predictive Maintenance: Machine learning algorithms can analyze historical performance data to predict when machinery will require maintenance, reducing downtime and maintenance costs.
- Process Optimization: By analyzing production data in real-time, MES can provide actionable insights on ways to optimize workflows or adjust parameters to improve product quality.
- Enhanced Decision-making: With data-driven insights, managers can make more informed decisions, adjusting strategies based on concrete evidence rather than intuition alone.
The ability to harness data in meaningful ways equips manufacturers to remain agile in a fast-paced industry, driving their competitiveness in the marketplace.
Cloud-Based MES Solutions
The advent of cloud technology has revolutionized how MES solutions are deployed and managed. Cloud-based MES options offer flexibility and scalability that traditional on-premises systems might struggle to match. Key advantages of cloud-based systems include:
- Cost Efficiency: Lower upfront costs and reduced need for extensive in-house IT infrastructure.
- Accessibility: Users can access the MES from anywhere, fostering collaboration and enabling remote monitoring of production processes.
- Scalability: Companies can scale their MES solutions according to their evolving needs—adding features or additional usage as their operations grow.
However, it is crucial to address potential challenges, such as data security and compliance with local regulations. But with proper measures, the benefits often outweigh the concerns, making cloud-based MES solutions an attractive option for businesses of all sizes.
"The future of manufacturing lies in the successful integration of MES with Industry 4.0 technologies, enabling smarter factories that adapt to their environments."
In essence, MES serves as the backbone of smart manufacturing, driving efficiency, quality, and responsiveness in a world intricately connected through Industry 4.0.
Best Practices for MES Implementation
Implementing a Manufacturing Execution System (MES) is not a walk in the park; it demands meticulous planning and foresight. Following best practices can mean the difference between a smooth implementation and a bumpy ride. Proper implementation can transform manufacturing operations, leading to improved productivity and quality. Here’s a closer look at some best practices critical in achieving successful MES integration.
Conducting a Needs Analysis
Before diving headfirst into an MES implementation, a thorough needs analysis is essential. This step ensures that the system aligns with the specific requirements of the manufacturing environment. Failing to do this can lead to costly mistakes, like selecting an MES that’s either overly complicated or too simplistic.
A needs analysis involves several key elements:
- Identifying Pain Points: Pinpoint challenges faced in production, such as bottlenecks, quality issues, or lack of visibility.
- Defining Goals: Setting clear objectives—be it reducing lead times, improving compliance, or increasing flexibility in operations.
- Engaging Stakeholders: Involving team members from production, IT, and management to gather diverse insights helps in creating a comprehensive requirements list.
This process is about digging deep and understanding not just the surface-level issues but the underlying causes. By doing so, organizations can make informed decisions that lead to better outcomes.
Choosing the Right MES Vendor
Picking a vendor is like choosing a partner; it requires careful consideration. The right MES vendor can often be the linchpin of successful implementation. Here are a few things to consider:
- Experience and Expertise: Look for vendors with a strong track record in your industry. They should understand the nuances and challenges you face.
- Flexibility and Customization: Make sure the solution can be tailored to fit unique processes and requirements.
- Support and Services: Assess the level of post-implementation support offered, including training and ongoing maintenance.
- Cost vs. Value: While it might be tempting to go for the lowest bidder, evaluating long-term benefits versus initial costs is crucial.
An informed choice now can prevent a headache later, positioning the company for sustainable growth and efficiency.
Training and Support for End-Users
Once the right system is in place, effective training becomes paramount. An MES is only as good as the people using it. Without adequate training, even the most sophisticated system can fall flat. Here are some considerations:
- Tailored Training Programs: Customize training sessions to address different roles within the organization. Operators might need hands-on training, while managers may benefit from analytical focus.
- Ongoing Support: Beyond initial training, setting up a support system for queries or issues that arise is vital.
- Feedback Mechanism: Encourage users to share their experiences and suggestions. This can often lead to discovering hidden potentials within the system.
Effective training fosters an environment where users are confident and capable, leading to higher utilization rates and better outcomes.
Continuous Evaluation and Improvement
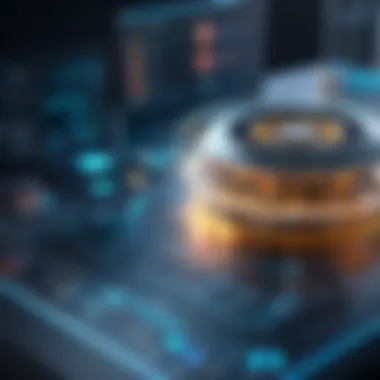
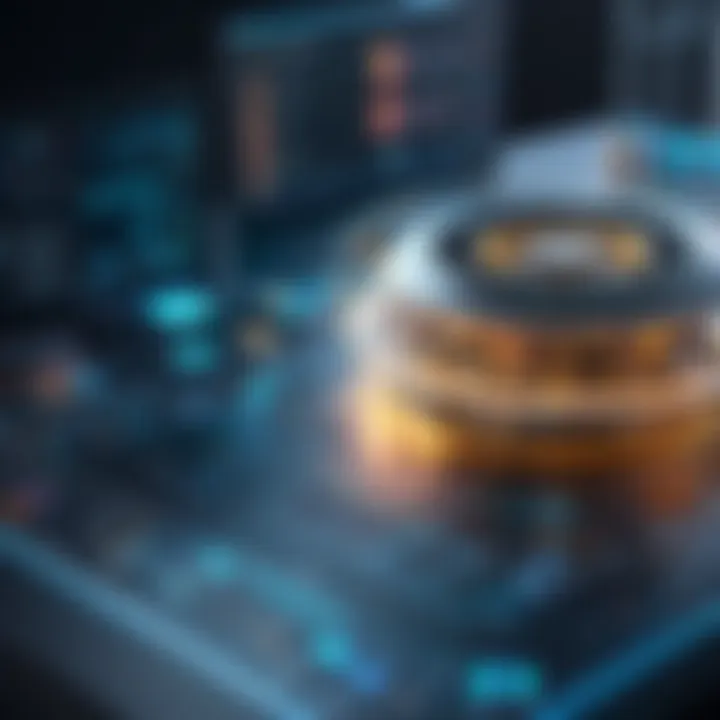
Implementing an MES doesn't stop at go-live. Continuous evaluation is necessary to adapt to changing business needs and technologies. Here’s why:
- Performance Metrics: Establish KPIs to monitor system performance. This allows for data-driven decisions to enhance productivity.
- Regular Updates: Keep abreast of software updates and enhancements that can improve performance and security.
- Iterative Improvement: Using feedback from end-users can highlight areas for optimization. This creates a cycle of improvement that enhances system utility.
Staying proactive in evaluating and refining MES implementation ensures it remains relevant and effective in an ever-evolving manufacturing landscape.
"In the world of MES, what you don't measure may escape attention, leading to missed opportunities for improvement."
By focusing on these best practices, organizations not only streamline their MES implementation but also pave the way for a resilient manufacturing operation. The right approach can lead to lasting benefits, transforming challenges into opportunities for growth and innovation.
Future Trends in MES
As the landscape of manufacturing continues to evolve, it’s crucial to keep an eye on the future trends in Manufacturing Execution Systems (MES). These trends not only illustrate the progression of technology but also bring essential innovations that drive the efficiency and adaptability of manufacturing processes. Understanding these trends allows organizations to prepare for shifts in operations and capitalize on the benefits they offer.
Artificial Intelligence Advancements
AI is no longer just a buzzword in the tech world; it’s deeply intertwined with the functioning of MES. The integration of artificial intelligence into MES is redefining how data is interpreted and actions are taken within manufacturing environments. For example, AI algorithms can automatically analyze production data to predict equipment failures before they happen, minimizing downtime.
Moreover, AI can enhance decision-making, offering insights that are rooted in vast amounts of data, a task beyond human capacity. The predictive analytics provided by AI helps in optimizing production schedules and resource allocation, ultimately improving operational efficiency.
In practical terms, MES systems equipped with AI capabilities enable businesses to:
- Anticipate issues before they escalate.
- Optimize supply chain management.
- Provide personalized user experiences through smart interfaces.
In short, these advancements make MES not just a reactive system but a proactive ally in the manufacturing sector.
Sustainability in Manufacturing Processes
Sustainability is becoming a cornerstone of modern manufacturing, and MES plays a vital role in this shift. Businesses are increasingly held accountable for their environmental impact, and the demand for sustainable practices is driving change across industries. Implementing MES helps manufacturers track and manage resource consumption more effectively, addressing sustainability from various angles.
For instance, MES can monitor energy usage, waste management, and material efficiency in real-time. This enhances the ability to identify inefficiencies and enables the implementation of more sustainable practices. By promoting responsible use of resources, companies not only adhere to regulatory standards but also enhance their reputation among environmentally conscious consumers.
Key sustainability benefits of MES include:
- Enhanced tracking of resource consumption.
- Reduction in waste through improved process control.
- Ability to report sustainability metrics effectively.
Thus, as sustainability becomes a business imperative, MES systems are positioned to support the quest for greener manufacturing environments.
Customization and Scalability of MES Solutions
The need for tailored solutions is paramount in today’s diverse manufacturing landscapes. Customization within MES allows companies to adapt their systems to meet specific operational needs without compromising overall functionality. Whether a business is a small bakery or a multinational car manufacturer, MES must meet unique requirements.
Moreover, the scalability of MES is equally crucial. Companies are often faced with rapid growth or the need to pivot their production strategies. A scalable MES solution can grow alongside the business, integrating new functionalities or additional processes without requiring significant overhauls. This adaptability makes it easier for organizations to remain competitive in a fast-paced market.
To summarize, customizing and scaling MES solutions promotes:
- Flexibility: Tailoring the system to fit specific workflows.
- Growth Support: Scaling capabilities as the company expands or diversifies its production lines.
- Cost Efficiency: Avoiding extensive costs associated with transitioning to an entirely new system.
With these advantages, businesses are more likely to experiment with new processes and technologies, leading to innovation and enhanced productivity.
Closure
The conclusion of this article provides a crucial wrap-up of our exploration into Manufacturing Execution Systems (MES). It serves as a focal point, bringing together various strands discussed throughout the text. As we summarized the benefits and challenges of MES implementation, it's evident that these systems play a pivotal role in driving operational efficiency within manufacturing settings. By harmonizing real-time data collection and advanced analytics, organizations can make informed decisions that foster better productivity.
One key insight is how MES offers a bridge between the factory floor and management, providing transparency across all levels of operation. This transparency in data has implications that go beyond mere numbers; it enables stakeholders to visualize processes, track performance, and identify bottlenecks, thus enhancing overall operational agility.
Effective deployment of MES can lead to a 20% reduction in operational costs, as evidenced by various case studies in industries ranging from automotive to pharmaceuticals.
Moreover, the challenges surrounding MES, such as integration with legacy systems and overcoming resistance to change, present both hurdles and opportunities for organizations. As businesses navigate these complexities, they aren’t just adopting technology; they are reshaping their corporate culture and operational frameworks to embrace a more data-driven approach.
Summarizing Key Insights
In summary, the journey into MES reveals several key insights:
- Integration is Vital: Successful MES deployment hinges on seamless integration with existing systems—both software and hardware.
- Employee Training: The workforce must be prepared to adapt to new technology, emphasizing the need for substantial training and support programs.
- Continuous Improvement: MES should be viewed as an evolving solution, necessitating regular updates and adaptations as technologies and business needs change.
- Data-Driven Decisions: With the capabilities of real-time monitoring and analytics, organizations can transform data into actionable insights.
These insights illuminate the multifaceted role that MES holds in modern manufacturing, serving as both a tool for enhancement and a framework for strategic growth.
The Future of MES in Manufacturing
As we gaze into the future of MES, several trends begin to surface. One prominent trend is the increasing integration of Artificial Intelligence (AI) into MES frameworks. The potential for AI to analyze vast datasets far exceeds human capability, allowing manufacturers to predict maintenance needs, optimize workflows, and even enhance product quality.
Additionally, sustainability in manufacturing processes is coming to the forefront. As industries face mounting pressure to decrease their environmental footprint, MES can support this endeavor through efficient resource management and waste reduction strategies.
In terms of scalability and customization, manufacturers are best positioned when equipped with versatile MES solutions tailored to their unique needs. Future MES systems are likely to offer flexible features that allow for tailored implementation, accommodating both small startups and large enterprises. This adaptability ensures that organizations can pivot as market demands evolve.
Thus, the future of MES isn’t just about coping with ongoing changes; it’s about leveraging those changes to propel innovation and efficiency in the manufacturing sector.