Exploring PCB Simulation: Techniques and Trends
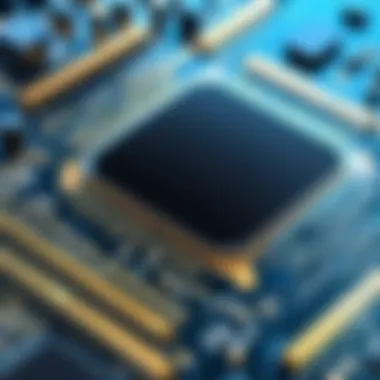
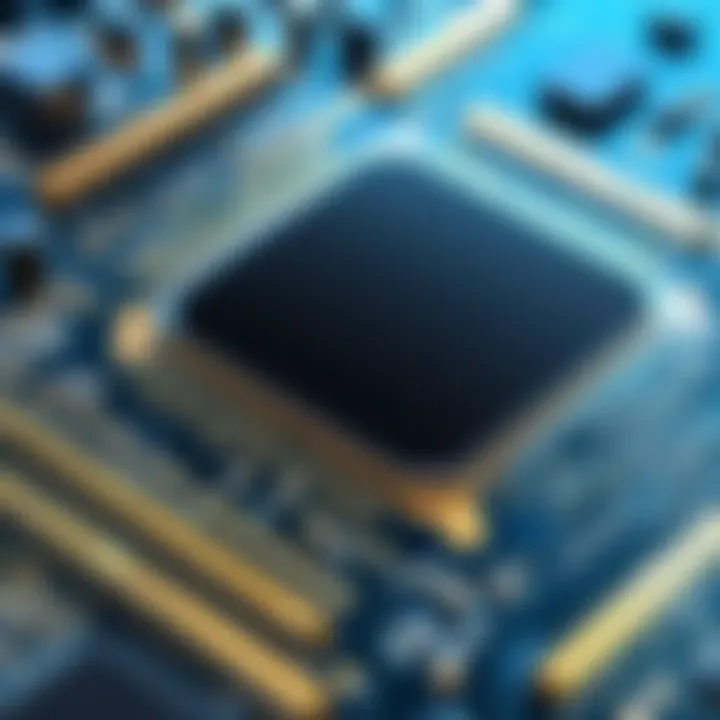
Intro
Printed Circuit Board (PCB) simulation has become an essential area of focus for professionals in the electronics design and manufacturing sectors. The process of simulating PCBs offers deep insights into performance and functionality before any physical prototypes are created. This not only enhances the reliability of the designs but also significantly reduces costs by minimizing errors during the production phase. This article serves as a comprehensive guide, unveiling various simulation techniques and tools, their applications, and addressing the core benefits they bring.
Understanding PCB simulation is imperative for both novices and experienced professionals. As electronics become more complex, the importance of adequate simulation grows. This guide will highlight the significance of these methods in verifying and optimizing layouts, thus pushing forward innovations in electronic products.
Software Overview
Software Description
The software used for PCB simulation varies widely, encompassing tools that span from basic schematic design applications to advanced electromagnetic simulation programs. Programs like Altium Designer and Cadence OrCAD provide robust environments for simulating electrical and physical attributes of PCBs. These tools let designers test their ideas in a virtual setting, allowing for adjustments and improvements before any layout goes into production.
Key Features
- Schematic Capture: Enables users to design their circuit schematics, ensuring that the connections and ports of components are accurately represented.
- Circuit Simulation: These tools can simulate real-world operating conditions and quickly evaluate the impact of changes to the design.
- Signal Integrity Analysis: This feature identifies potential issues with signal degradation or interference, which is paramount in high-speed designs.
- Thermal Management: Some software includes thermal simulation, allowing designers to analyze heat distribution across the board, aiding in effective thermal management.
- Design Rule Checks (DRC): Automated checks help enforce the rules and regulations tied to PCB manufacturing, catching errors before they lead to costly mistakes.
User Experience
User Interface and Design
A user-friendly interface is crucial in making PCB simulation tools accessible to all levels of users. The dashboards in software like Eagle PCB or KiCad allow easy navigation and visualization of designs. Intuitive drag-and-drop features enhance user experience, streamlining the workflow from schematic capture to final design verification. Moreover, tutorials and help sections embedded within these platforms help beginners familiarize themselves with complex functions.
Performance and Reliability
Performance is a measure of how efficiently the software operates under various loads. A reliable simulation tool can handle larger, more complex designs without lag or crashing. High-quality software, such as Mentor Graphics PADS, is tested rigorously to ensure that users can trust simulation results. The integrity of these results can significantly influence design decisions. Consistency in performance also helps foster an environment of continual improvement in design methodologies.
"Thorough PCB simulation can lead to designs that outperform initial expectations, thus providing a competitive edge in a fast-paced market."
By delving into the tools and methodologies associated with PCB simulation, professionals can cultivate deeper knowledge and skill, leading to effective and error-reduced designs.
Prolusion to PCB Simulation
PCB simulation stands as a pivotal aspect within the electronics design domain. It offers engineers and designers the ability to test and validate their ideas before actual fabrication. This process is crucial in achieving a sound design that meets performance specifications while minimizing errors.
Definition and Relevance
PCB simulation refers to the use of specialized software to predict the behavior of printed circuit boards under various conditions. This involves assessing electrical performance, thermal behavior, and even mechanical stress. The relevance of simulation lies in its ability to save both time and resources. By identifying potential issues early in the design process, teams can avoid costly redesigns or production delays. Moreover, utilizing simulation effectively leads to better-informed decisions, ultimately enhancing product reliability.
Historical Context
The journey of PCB simulation began in the mid-20th century, coinciding with the rapid evolution of electronics. Early simulations were rudimentary, often limited to simple circuit calculations. However, as technology advanced, so did the tools. By the 1980s, sophisticated software emerged, enabling complex simulations that provided deeper insights into design challenges. This evolution reflects a broader trend in the industryโan increasing reliance on digital solutions to improve efficiency and effectiveness in design processes. With the rise of computational power in the 21st century, PCB simulation became essential, allowing for intricate designs that align with modern electronics demands.
"Simulation in PCB design is not just a tool, but a necessity for achieving optimal performance in todayโs electronics."
Through examining the definition and the historical context, it becomes evident that PCB simulation is not merely a technical element; it is foundational in shaping how modern electronics are conceived, developed, and realized.
Fundamental Concepts of PCB Design
Understanding the fundamental concepts of PCB design is crucial for anyone involved in electronics. This section lays the groundwork for grasping how printed circuit boards function and their layout's critical aspects. PCB design not only affects the performance of electronic devices but also influences manufacturability and reliability. A profound comprehension of these concepts helps in making informed design choices, ultimately leading to better product outcomes and success in the market.
Overview of Printed Circuit Boards
Printed circuit boards are essential in connecting various electronic components. At their core, PCBs serve as a foundation for mounting and interconnecting electronic parts, ensuring they operate efficiently. Todayโs PCBs can be single-sided, double-sided, or multilayered, made from materials such as fiberglass or epoxy resin. The selection of material greatly impacts the board's electrical and thermal performance.
The design of a PCB involves creating printed pathways that connect different components like resistors, capacitors, and microcontrollers. Each pathway, or trace, carries electrical signals, forming a communication network within the device. This intricate web of connections is vital for the functionality of devices ranging from simple gadgets to advanced computing systems.
A well-designed PCB reduces signal interference, improves durability, and ensures manufacturability. When designing PCBs, attention must be paid to voltage levels, signal types, and potential sources of interference. Understanding these factors contributes to a reliable and efficient design, which is critical for any application.
Key Components in PCB Layout
The PCB layout consists of various components, each serving a unique purpose. Key elements include:
- Traces: Thin paths that connect different components on the board, like wires in a circuit.
- Pads: Small metal areas where components are soldered onto the PCB, ensuring a solid electrical connection.
- Vias: Plated holes that allow traces to connect between different layers of a multilayer PCB.
- Silkscreen Layer: A layer that contains text and symbols for identifying components, aiding both assembly and debugging processes.
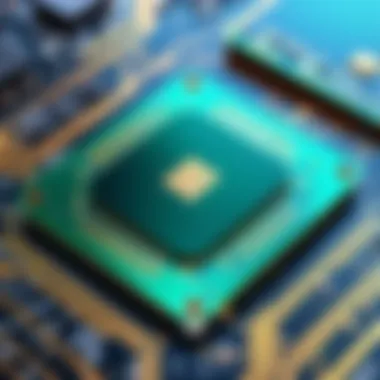
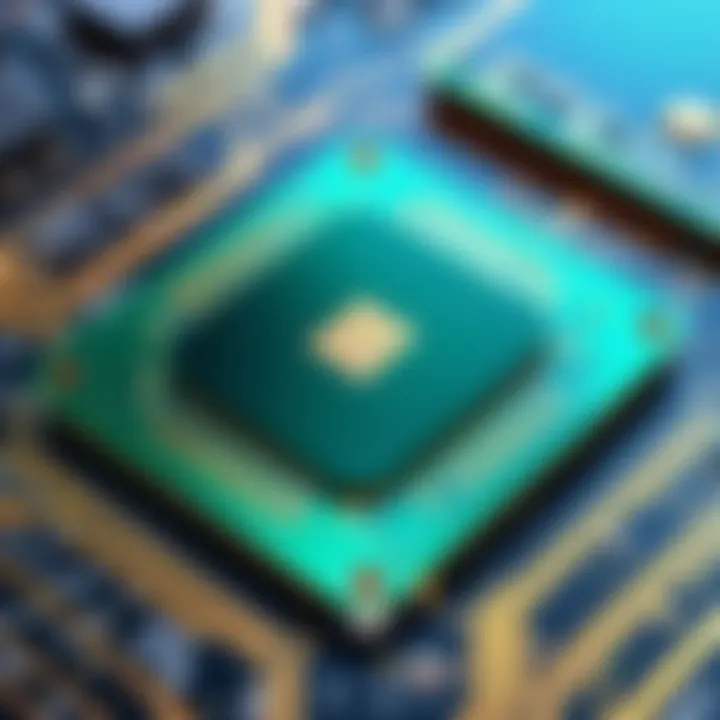
When laying out a PCB, it is crucial to maintain clearances between traces and stray elements to prevent accidental shorts or interference. Proper positioning of components not only enhances manufacturability but also improves overall performance. Designers often utilize software tools to create these layouts, allowing for simulations that help identify potential issues before production.
In summary, the fundamental concepts of PCB design set the stage for effective designs that meet both functional and production requirements. By understanding the intricacies of PCBs and their key components, professionals can develop optimized layouts that enhance product performance and reliability.
Types of PCB Simulation Techniques
The types of PCB simulation techniques are critical in understanding how to effectively design and validate printed circuit boards. These techniques serve as the foundation for achieving robust and reliable PCB designs. Each simulation technique offers unique insights into the performance of a PCB under various conditions. Employing these techniques not only enhances design accuracy but also minimizes potential issues that could arise during manufacturing and operation.
Signal Integrity Simulation
Signal integrity is a vital aspect of PCB design, especially as circuit speeds continue to increase. Signal integrity simulation focuses on analyzing the electrical signals traveling through the PCB. It addresses issues such as reflections, crosstalk, and propagation delays.
When signals ascend to higher frequencies, they become more susceptible to degradation. Poor signal integrity can lead to data corruption and system malfunctions. By utilizing signal integrity simulation, designers can forecast potential conflicts in signal paths and make adjustments before physical prototyping. This ensures that important signals maintain their integrity throughout the PCB.
Key Benefits:
- Early Detection of Issues: Identifying potential signal integrity problems during the simulation phase reduces the chances of redesign later.
- Enhanced Performance: Optimizing the PCB design for signal integrity results in better system performance overall.
Thermal Simulation
Thermal management is another essential aspect of PCB design. Thermal simulation is used to predict temperature distribution within the PCB, which is crucial for ensuring that components operate within safe limits. When components generate heat, failure can occur if the heat is not properly dissipated.
Thermal simulation enables designers to visualize how heat flows through the board, identify hotspots, and determine the effectiveness of thermal management solutions such as heatsinks or thermal vias. Simulating these conditions can support effective decisions about component placement and cooling methods, promoting reliability and longevity in electronic devices.
Considerations:
- Component Placement: The layout of components significantly affects thermal performance. Simulation helps to optimize their arrangement.
- Cooling Solutions: Determining whether passive or active cooling solutions are necessary can be evaluated through thermal simulations.
Electromagnetic Simulation
Electromagnetic simulation examines how electromagnetic fields interact with the PCB and its components. It is essential for understanding the effects of electromagnetic interference (EMI) and electromagnetic compatibility (EMC). With the proliferation of wireless technologies and high-speed digital circuits, analyzing electromagnetic behavior has become imperative.
Using electromagnetic simulation allows designers to assess unintended emissions or susceptibility to external noise. This ensures compliance with regulatory standards and enhances product reliability. Designers can explore different shielding techniques and PCB layouts to mitigate potential interference.
Key Points to Remember:
- Compliance with Standards: Adhering to EMI/EMC regulations through simulation helps avoid costly redesigns and ensures product marketability.
- Design Optimization: By evaluating the electromagnetic behavior early in the design phase, engineers can make informed choices that enhance performance and minimize disruption.
Effective use of various simulation techniques can significantly improve the PCB design process, addressing potential issues from the start and ultimately leading to better end products.
Simulation Tools Overview
In the realm of PCB simulation, tools play a pivotal role in designing, analyzing, and validating printed circuit boards. Simulation tools are essential because they provide insights into how a design will behave under real-world conditions. By accurately simulating signals, thermal characteristics, and electromagnetic effects, these tools aid in preventing costly errors that could arise during physical production. Therefore, selecting the right simulation tools can significantly enhance the efficiency and effectiveness of the design process.
Common Simulation Software
SPICE
SPICE, which stands for Simulation Program with Integrated Circuit Emphasis, is widely regarded as a cornerstone in the field of electronic simulation. One of its key characteristics is its ability to perform detailed circuit analysis, allowing engineers to simulate the performance of circuits before implementation. SPICE is a beneficial choice for PCB simulation due to its versatility and extensive model libraries, which cover a wide range of components.
A unique feature of SPICE is its compatibility with various other tools, notably in mixed-signal circuit simulations. This integration facilitates a more comprehensive view of design performance.
However, SPICE does have disadvantages. Its steep learning curve may deter newcomers, and sometimes it requires significant computational resources for complex simulations, which can slow down the process in certain cases.
HSPICE
HSPICE, a commercial variant of SPICE, is recognized for its accuracy and performance in simulating analog circuits. Known for its robust analysis options, HSPICE allows users to conduct comprehensive simulations with a high degree of precision. Many companies prefer HSPICE due to its advanced features like Monte Carlo simulations and optimization capabilities.
A unique feature of HSPICE is its ability to handle large-scale simulations efficiently.
Despite its advantages, HSPICE can be costly, which may restrict its use to larger enterprises. Additionally, some users may still find its interface less intuitive compared to other simulation tools available in the market.
Mouser Electronics
Mouser Electronics provides a range of simulation tools that are particularly useful for engineers at various levels of expertise. Its emphasis on educational resources makes it an attractive platform for beginners. The key characteristic of Mouser is its extensive catalog of components, alongside integrated simulation capabilities that allow users to see how parts perform in simulated environments.
A unique feature is Mouser's user-friendly interface, which makes accessing simulation tools easy for novice engineers.
On the downside, while Mouser might be excellent for educational purposes, its simulation depth may not match those offered by specialized tools like SPICE or HSPICE. Users seeking advanced features may find Mouser less comprehensive for larger design projects.
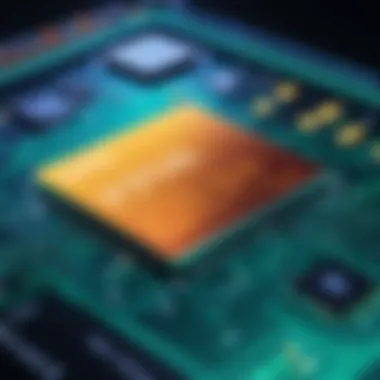
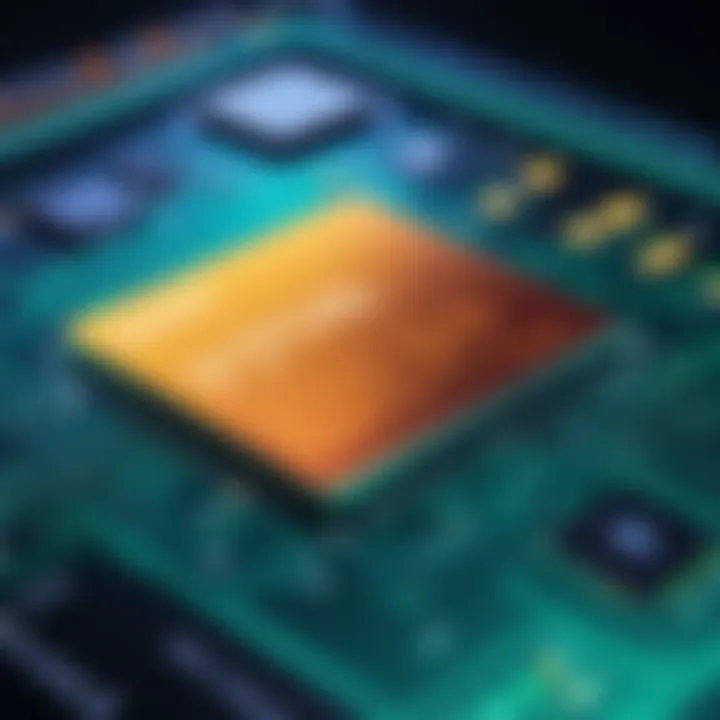
Cloud-Based Simulation Platforms
Cloud-based simulation platforms are gaining popularity in PCB design due to their flexibility and collaborative capabilities. These platforms allow multiple users from different locations to work on the same project concurrently. Notable benefits include reduced hardware costs and real-time updates. Additionally, they offer access to powerful computing resources, which can enhance simulation speed and efficiency.
Key considerations include internet dependency and potential issues with data security. However, with the rise of cloud technology, many providers are implementing robust security measures to protect sensitive information. Overall, cloud-based platforms are becoming an integral part of the modern PCB design toolkit, providing both convenience and efficiency.
Implementation of PCB Simulation
The implementation of PCB simulation is a crucial phase in the design workflow. This step combines methodologies, tools, and expertise to create, test, and refine PCB designs before physical prototypes are made. Understanding how to effectively implement PCB simulations can significantly enhance the quality of the final product. By simulating various scenarios, engineers can predict performance outcomes, identify potential faults, and make informed design decisions early in the process.
Setting Up Simulation Parameters
Setting up simulation parameters is essential for achieving accurate results. This process involves defining the parameters that will guide the simulation, such as:
- Frequency Range: It is important to determine the appropriate frequency range for the simulation based on the application of the PCB. High-frequency signals may require more detailed models to accurately assess performance.
- Component Models: Accurate modeling of components, which includes resistors, capacitors, inductors, and semiconductors, is necessary. These models should reflect real-world behavior to provide valid results.
- Boundary Conditions: These establish how the simulated environment interacts with the PCB. Factors like air gaps, soldering interfaces, and thermal conditions should be considered.
Proper parameter settings ensure that the simulation reflects realistic operating conditions. If set incorrectly, the simulation results may lead to misguided design choices.
Conducting Simulations and Interpreting Results
Once the simulation parameters are in place, conducting the simulations is the next step. This involves running the defined scenarios and observing the system's response. Here are key factors to consider:
- Simulation Duration: Longer simulations can yield more accurate results but may consume more computational resources.
- Data Analysis: After the simulation, results must be thoroughly analyzed. This includes identifying any discrepancies from expected performance. Noteworthy aspects often evaluated are signal integrity, thermal effects, and electromagnetic interference.
- Iterative Refinement: Simulation is rarely a one-time process. It is crucial to refine designs iteratively. Review results, adjust design, and re-simulate to assess improvements.
Effective interpretation of simulation results allows design teams to make adjustments that enhance product integrity, leading to reduced costs and improved performance.
In summary, the implementation of PCB simulation encompasses setting up accurate parameters and conducting detailed simulations. Understanding these steps lays a strong foundation for generating reliable designs in the electronics industry. This systematic approach can lead to innovations while addressing common challenges in PCB design.
Benefits of PCB Simulation
PCB simulation provides several essential advantages in the design and development of printed circuit boards. With rising complexities in electronic devices, simulation has emerged as a pivotal process in ensuring the reliability and functionality of PCBs. By offering an understanding of how designs will behave under various conditions, PCB simulation plays a crucial role in modern electronics design methodologies. This section elaborates on specific benefits, focusing primarily on error reduction in design and cost-effectiveness in production.
Error Reduction in Design
Designing PCBs involves intricate layouts and connectivity. Small mistakes can lead to significant failures in the final product, causing costly delays and rework. PCB simulation minimizes these risks by allowing engineers to visualize potential issues before physical prototypes are created.
When performing simulations, designers can analyze various factors, such as electrical currents, voltages, and thermal effects. By running multiple scenarios, potential problems can be identified early. Some of the common issues that simulation helps address include:
- Short circuits: Finding unintended connections between traces.
- Signal degradation: Understanding how signals can be affected as they travel through the board.
- Thermal issues: Identifying hot spots that could cause components to fail.
- Design violations: Ensuring compliance with specific design rules and standards.
Implementing PCB simulation effectively reduces the probability of design errors, making it a fundamental tool for enhancing overall quality.
"Simulation enables engineers to discover design flaws that might not be evident until much later in the development cycle."
Cost-Effectiveness in Production
The cost implications of electronic product development are significant. Reducing costs while maintaining quality is a goal for many companies. PCB simulation provides a pathway to achieve this balance. By investing time in simulations during the design process, businesses can avoid the higher costs associated with manufacturing flaws.
There are several ways in which PCB simulation contributes to cost-effectiveness:
- Early identification of issues: Fixing problems at the simulation stage is considerably cheaper than making changes to a physical board after manufacturing.
- Fewer prototypes needed: Simulations can lead to fewer prototype iterations. This saves on material costs and time resources.
- Optimized designs: Simulations can optimize layouts, which may lead to using fewer materials or smaller, less expensive components.
- Reduced warranty claims and returns: Higher reliability in the final product decreases the likelihood of return due to failures, further saving costs associated with support and replacements.
Challenges in PCB Simulation
PCB simulation plays a critical role in modern electronics design, yet it is not without its challenges. Understanding these challenges is key for engineers and designers aiming to optimize their workflows effectively and deliver high-quality products. The potential pitfalls in PCB simulation are numerous, and they often underline the complexities involved in accurately modeling electronic components and systems.
Modeling Complex Components
One of the primary challenges in PCB simulation lies in modeling complex components. As electronic devices evolve, they incorporate various functions and features that interact in intricate ways. This complexity makes it difficult to create accurate models that reflect real-world performance. For example, components such as multi-layer capacitors or integrated circuits exhibit behaviors that are not straightforward to simulate. The non-linear characteristics of these devices often require advanced models and extensive computational resources to replicate accurately.
Inaccuracies in these models can lead to significant design errors. A slight deviation in component characteristics can cause cascading failures in the overall circuit design, leading to performance issues and costly revisions in the later stages of development. Thus, careful attention to component models is crucial for achieving reliable simulations and ultimately successful PCB designs.
Performance Limitations of Tools
Another issue frequently encountered is the performance limitations of available simulation tools. Many designers utilize software like SPICE or HSPICE for their simulation needs, but these tools have inherent restrictions. While they provide a good starting point, they may struggle with extensive simulations that require high fidelity. This can become particularly evident in larger PCB designs with multiple interconnected components that demand significant processing power and memory.
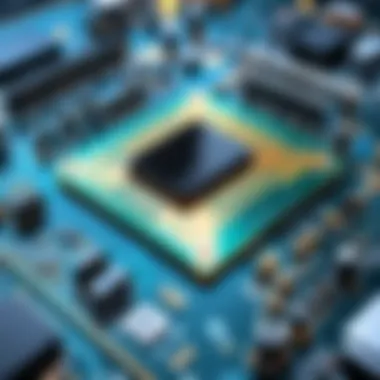

Moreover, the interface of some simulation tools can be convoluted, hindering user experience and making it difficult to adjust parameters or interpret results. If a tool lacks versatility or efficiency, it can frustrate designers, leading to sub-optimal outcomes in their simulations.
"Understanding modeling complexities and tool limitations is essential for accurate PCB simulation outcomes."
In summary, challenges in PCB simulation, particularly with modeling complex components and performance limitations of tools, require careful consideration and thoughtful approaches. Designers must take a proactive stance to address these obstacles, ensuring they choose the right tools and methods for creating accurate and efficient PCB designs. With thorough attention to these challenges, teams can better harness the advantages of PCB simulation, paving the way for higher quality products.
Future Trends in PCB Simulation
The realm of PCB simulation is constantly evolving, driven by technological advancements and the increasing complexity of electronic devices. Staying abreast of future trends is essential for IT professionals, software developers, and businesses aiming to maintain a competitive edge. Understanding how these trends shape simulation methods and tools can greatly support better design processes.
Advancements in AI and Machine Learning
Artificial intelligence and machine learning are transforming PCB simulation in significant ways. These technologies can analyze large datasets, uncover design patterns, and offer predictive insights that were previously unavailable.
One of the main benefits of integrating AI is the automation of time-consuming tasks. By leveraging machine learning algorithms, designers can more quickly identify and resolve potential design flaws. This not only enhances the efficiency of the design process but also helps in achieving higher reliability in the final product.
Moreover, AI can support optimization processes by simulating numerous design iterations within a shorter time frame. This allows engineers to explore a wider range of possible solutions before settling on a final design. As a result, PCB layouts can be fine-tuned to maximize performance while minimizing costs. According to a recent study, companies that implement AI-driven simulation tools reported a 30% reduction in design cycle time.
Integration with Other Design Tools
The trend toward integration with other design tools is taking shape as PCB simulation becomes more interconnected with broader engineering disciplines. Designers are increasingly utilizing platforms that combine schematic capture, PCB layout, and simulation into one cohesive workflow. This integration can facilitate a more holistic approach to design.
Several popular design environments include Altium Designer, KiCad, and OrCAD. They enable seamless transitions between different aspects of PCB design, allowing for simultaneous adjustments across various elements. This collaboration fosters greater communication between electrical engineering and mechanical design teams, leading to more informed decisions and potentially better overall product outcomes.
Key Considerations:
- Software Compatibility: Ensure that simulation tools are compatible with other design software in use.
- Data Sharing: Establish protocols for data sharing between tools to streamline the design process.
- Interdisciplinary Collaboration: Foster collaboration between different engineering disciplines to enhance design quality.
Moving forward, the importance of integrating PCB simulation tools with other design software cannot be overstated. By embracing these advancements, engineers can pursue optimized, efficient workflows that elevate product development.
Case Studies of Successful PCB Simulations
Case studies are essential to understanding the practical impact of PCB simulation in real-world scenarios. They provide insight into how various industries apply simulation techniques to improve their designs and operations. These examples illustrate the benefits of PCB simulations, showcasing the efficiency gained and the errors avoided throughout the design process.
By studying specific instances where PCB simulation played a pivotal role, organizations can learn to navigate challenges effectively. They can replicate successful strategies while avoiding common pitfalls encountered in the industry. The knowledge gained from these case studies serves as a valuable resource for both newcomers and seasoned professionals.
Industry-Specific Applications
Different industries bring unique demands to PCB design. In consumer electronics, manufacturers often focus on shrinking component sizes while maintaining performance. Simulation tools help them predict thermal behavior and signal integrity in compact boards. This can lead to innovative designs that pack more functionality into a smaller space.
In the automotive sector, PCB designs must endure harsh environments. Here, thermal simulation can predict how heat impacts critical components in a vehicle. Notable systems include the Tesla Model S, which employs advanced PCB simulation to optimize the battery management system. This not only enhances performance but also extends the lifespan of components, leading to significant cost savings over time.
Aerospace applications also highlight the importance of PCB simulation. Reliability and performance in flight systems cannot be compromised. Boeing and Airbus use simulation extensively to ensure that their PCBs meet rigorous safety and performance standards. The consequences of failure in this sector can be dire, making simulations a key component of their design process.
Innovative Approaches to Common Problems
PCB simulation tackles various challenges, such as signal integrity issues or thermal management problems. Innovative approaches often arise when teams confront these hurdles. One effective strategy is the integration of multiple simulation types. For example, coupling thermal and electromagnetic simulations can provide a more holistic view of how a PCB will perform under various conditions.
Such effectiveness is reflected in designs like the Intel processors. The engineers at Intel combine multiple simulations to address power distribution and electromagnetic interference comprehensively. This approach has led to higher processor speeds while maintaining lower power consumption, resulting in overall better products.
Moreover, adopting machine learning methods is becoming increasingly popular in PCB simulation to predict outcomes based on previous data. This method allows for rapid design iterations without the need for extensive trial and error, significantly shortening design cycles. Companies like NVIDIA have incorporated AI to identify and rectify design flaws early on, allowing for more efficient use of resources and time.
Culmination
The conclusion of this article serves as a means to consolidate the key insights and findings shared throughout the exploration of PCB simulation. It emphasizes the significance of integrating simulation into the PCB design process. PCB simulation acts not just as a tool for verifying designs but also as a strategy for enhancing overall product reliability and efficiency. By applying various simulation techniques, designers can anticipate potential issues, optimize layouts, and significantly reduce design iterations.
Recap of Key Points
To reinforce the understanding of PCB simulation, the following points are crucial:
- Definition and Relevance: PCB simulation is integral to modern electronics design. It allows for the assessment of performance before physical prototypes are created.
- Types of Simulation Techniques: Different simulation methods, including signal integrity, thermal analysis, and electromagnetic simulation, each serve distinct purposes in optimizing design.
- Software Tools: Popular tools such as SPICE and HSPICE play pivotal roles in facilitating effective simulations.
- Benefits: The primary advantages include reduced errors, lower costs in production, and improved product performance.
- Challenges: Modeling complex components and the limitations of current simulation tools must be acknowledged as ongoing challenges.
- Future Trends: The advancement of AI and machine learning presents opportunities for even more sophisticated simulations, reinforcing the need for continuous innovation.
These points not only encapsulate the essence of PCB simulation but also highlight its growing significance in the field of electronics design.
Call to Action for Future Research
As PCB simulation continues to evolve, there are vital areas where further investigation is necessary. It is recommended that professionals in the industry focus on:
- Enhancing Simulation Accuracy: Research should emphasize developing improved modeling techniques to reflect real-world conditions more closely.
- Integrating Emerging Technologies: As AI and machine learning make headway into simulation processes, studying their implications and applications can yield significant benefits.
- Standardizing Simulation Practices: As the industry adapts, establishing common standards can promote consistency and reliability in PCB design.
- Expanding Educational Resources: Creating more comprehensive training materials and workshops will empower designers at all levels to utilize simulation effectively.
These initiatives will bridge the existing gaps and foster innovation, ultimately enhancing the capabilities and outcomes of PCB designs.