SAP's Impact on Modern Manufacturing Efficiency
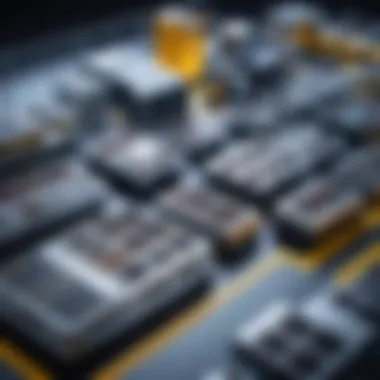
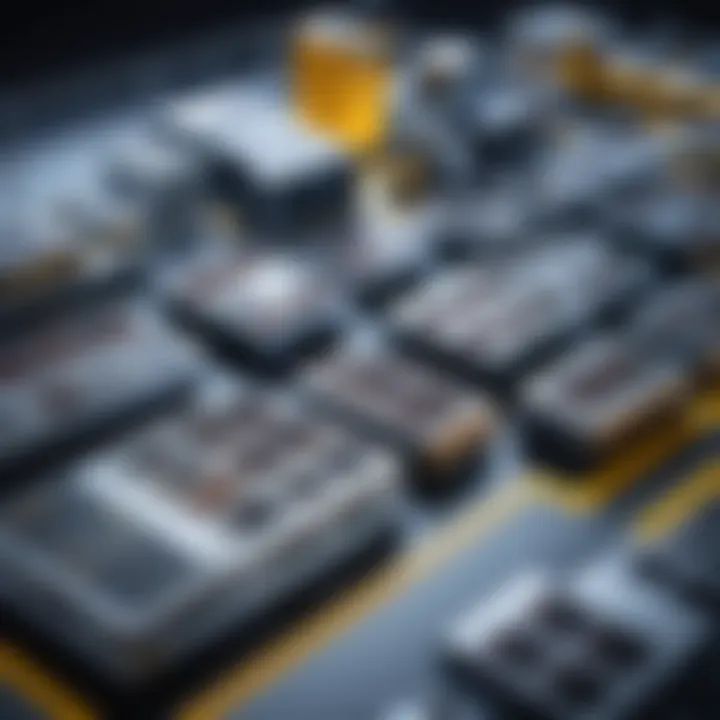
Intro
In a world where factories are becoming smarter and more connected, the role of sophisticated software systems like SAP cannot be understated. The manufacturing sector is undergoing a transformation that necessitates an agile approach to operations, and SAP is at the forefront of this change. This article delves into how SAP integrates seamlessly with manufacturing processes, driving efficiency and enhancing productivity.
SAP stands as a pillar in this digital landscape, offering an array of modules tailored to meet the unique needs of various manufacturing environments. From facilitating supply chain management to optimizing production schedules, understanding the underlying mechanisms of SAP is crucial for any organization looking to elevate its manufacturing game.
By examining the specific features, user experiences, and real-world applications of SAP, we will reveal the vital role this software plays in modern manufacturing settings. Let's embark on this journey to uncover how SAP catalyzes improvement, streamline operations, and ultimately powers decision-making processes in industrial settings.
Software Overview
Software Description
SAP, or Systems, Applications, and Products in Data Processing, is a comprehensive software suite that addresses the complex requirements of manufacturers across the globe. This system is designed to manage various aspects of business operations, integrating data from different departments to ensure smooth workflows. It offers tailored solutions that vary from inventory management to production scheduling, effectively acting as the central nervous system for manufacturing enterprises.
Key Features
SAP's modular design is one of its standout features. Here are some of its key components that are particularly relevant to manufacturing:
- SAP Production Planning (PP): This module aids in production scheduling and manages data related to manufacturing processes. It helps businesses track their production while enabling real-time adjustments.
- SAP Material Management (MM): Central to supply chain operations, MM takes care of inventory, procurement, and logistics, ensuring that materials flow smoothly across the production line.
- SAP Quality Management (QM): Ensuring product quality is ubiquitous in manufacturing. The QM module helps establish quality standards, conduct inspections, and manage compliance.
- SAP Supply Chain Management (SCM): This feature optimizes the entire supply chain, assessing demand and capacity to minimize waste and maximize output.
"The integration of SAP into manufacturing processes transforms raw data into operational insights, making it not just a tool but a vital strategic partner for businesses."
User Experience
User Interface and Design
A well-crafted user interface lies at the heart of effective software utilization. SAP invests significantly in ensuring its interface is both intuitive and functional. Users often note that while the initial learning curve can be steep, the design prioritizes navigation ease and accessibility. With dashboards customized for various roles, information is at your fingertips, quickly transforming complex data into actionable insights.
Performance and Reliability
In the fast-paced environment of manufacturing, speed and dependability are paramount. SAP delivers robust performance, designed to handle large amounts of data consistently without lag. Organizations often experience increased uptime and operational efficiency, making SAP an attractive choice for those who need reliable software to support high-stakes operations.
As we continue exploring the many facets of SAP's role in manufacturing, the discussion will include the hurdles organizations encounter during its implementation and how they can navigate these challenges to fully realize the software's potential.
Prologue to SAP in Manufacturing
In today's fast-paced industrial world, understanding SAP (Systems, Applications, and Products in Data Processing) and its role in manufacturing is crucial for both large-scale organizations and nimble small businesses. This section sets the stage by emphasizing why SAP systems have become indispensable in modern production environments and how they enhance operational efficiency.
By implementing SAP solutions, manufacturers can streamline processes, minimize waste, and improve overall output. These systems centralize critical data, making it easier for different functions to share information seamlessly. With such systems in place, a manufacturer can respond swiftly to market changes or production challenges, such as supply chain disruptions or demand shifts.
Furthermore, SAP offers various modules specifically designed for different aspects of production, such as production planning and quality management. This specialization greatly enhances a company’s ability to monitor and control workflows effectively. Moreover, as the manufacturing landscape continues to evolve with new technologies, SAP provides the framework necessary to adapt, thus allowing companies to remain competitive in an ever-changing market.
Overview of SAP Systems
SAP systems comprise a wide range of software solutions tailored for different industries, with manufacturing being a primary focus. These systems can integrate various functions such as finance, human resources, and logistics into a single framework. This integration is pivotal, as it ensures that stakeholders across departments have access to real-time data, leading to informed decision-making.
A point worth noting is the modular nature of SAP. Organizations can adopt specific modules based on their unique needs and expand their systems over time. For instance, a manufacturing firm might start with modules focusing on production planning and materials management, later branching out into quality management or plant maintenance as they scale operations.
In summary, SAP systems are not merely tools; they bridge the gap among processes, creating a cohesive operational strategy.
The Evolution of Manufacturing Processes
Manufacturing has come a long way since the days of assembly lines, and technology has been at the forefront of this transformation. The evolution started with mechanization and advanced through stages of automation and, more recently, digitization. Each phase has brought about significant changes in how products are conceptualized, designed, and produced.
With the advent of Industry 4.0, manufacturing is now on the brink of yet another technological revolution. This fourth industrial revolution hinges on the principles of smart connectivity, using IoT devices and real-time analytics. SAP plays a pivotal role in this transition by empowering manufacturers with tools to harness data effectively.
It's essential to recognize that the evolution towards more intelligent manufacturing processes is not merely about adopting new technologies; it requires rethinking old paradigms. Companies must embrace change management, ensuring that every employee understands how SAP will enhance their work rather than viewing it as an imposition.
This evolution reshapes expectations—today's manufacturing processes are no longer just about producing goods but about creating value through innovation, responsiveness, and sustainability.
"In an era where agility is key, knowing how to leverage SAP systems effectively becomes a driving force for success in manufacturing."
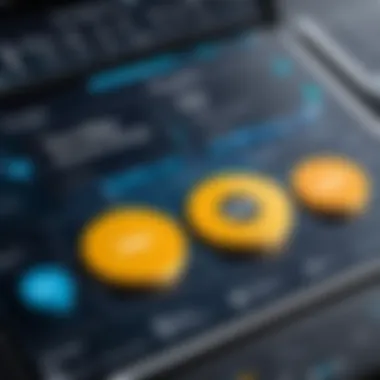
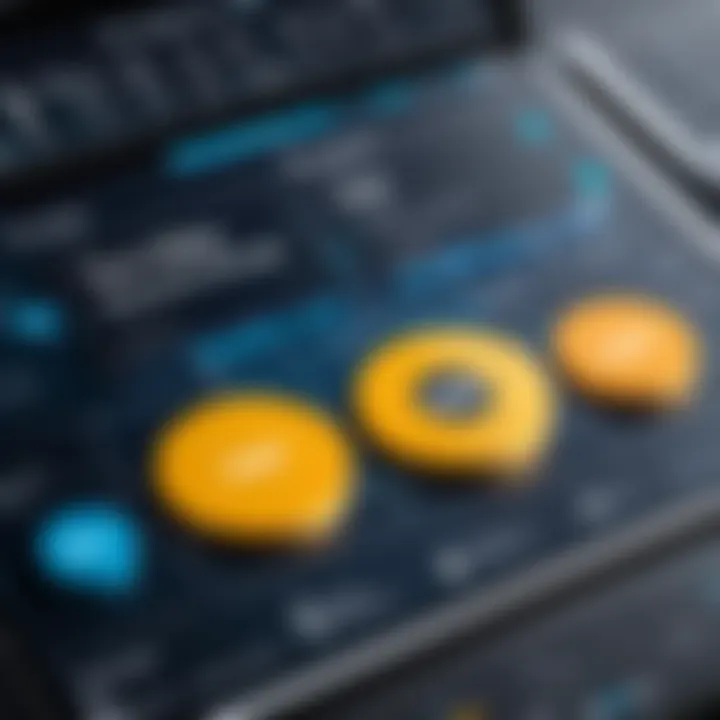
Core SAP Modules for Manufacturing
Understanding the Core SAP Modules for Manufacturing isn't just a technical necessity; it’s a crucial component that can significantly shift the paradigm of how industries operate today. These modules form the backbone of SAP's capabilities in the manufacturing sector, providing a seamless integration of processes that can drive substantial improvements in both efficiency and productivity. Each module targets specific aspects of manufacturing operations, ensuring that businesses can optimize their functions to meet the fast-paced demands of today’s market.
Production Planning and Control
The Production Planning and Control module serves as a vital aspect of SAP’s offerings for manufacturers. This tool allows organizations to design, execute, and oversee production processes with pinpoint accuracy. By utilizing real-time data, manufacturers can plan their production schedules to align more closely with resource availability and demand forecasts.
- Key Features:
- Detailed scheduling and capacity planning to maximize production lines.
- Integrated demand planning that updates in real-time with changing market conditions.
- Tools for tracking production orders from inception to completion.
The impact of effective production planning cannot be understated. It reduces lead times, minimizes wastage, and ultimately ensures that inventory levels remain at optimal levels, thereby preserving resources. Companies that harness this module often see a notable increase in throughput, enabling them to deliver products to market swiftly.
Materials Management
Materials Management is yet another cornerstone module in SAP’s manufacturing framework. It effectively handles procurement, inventory, and logistics processes, streamlining how materials are acquired, stored, and dispatched. This module fosters a transparent relationship between suppliers and manufacturers, crucial for just-in-time (JIT) manufacturing practices.
- Benefits:
- Improved inventory accuracy through real-time tracking.
- Automatic generation of procurement proposals based on inventory levels and consumption trends.
- Enhanced vendor management capabilities which aid in performance reviews and audits.
Adopting a robust materials management system enables organizations to cut down on excess stock and manage working capital more efficiently. It’s almost like having a digital assistant that knows exactly what you need, when you need it, thus reducing operational headaches.
Quality Management
When it comes to Quality Management, SAP provides tools designed to ensure that products meet regulatory standards and customer expectations. This module encompasses quality planning, inspection, and control, aiming to build a culture of quality that resonates throughout the organization.
- Implementation Tips:
- Integrate quality checks at every stage of the production process, rather than at the end.
- Utilize data analytics to identify trends in quality issues and develop proactive solutions.
- Encourage a feedback loop from customers to continuously improve quality standards.
An emphasis on quality management not only sustains customer satisfaction but also reinforces the brand’s reputation in the marketplace. Knowing that quality is assured from the start often allows companies to move ahead with confidence.
Plant Maintenance
Finally, the Plant Maintenance module is indispensable for manufacturers looking to monitor and enhance the operability and longevity of their equipment. This tool provides functionalities for preventive maintenance as well as reactive maintenance management, which can be critical for ensuring continuous production.
- Essential Features:
- Maintenance planning and scheduling to avoid unplanned downtime.
- Real-time reporting on equipment status and maintenance history.
- Cost tracking associated with maintenance activities.
Effective plant maintenance not only extends the lifecycle of machinery but also reduces overall maintenance costs. By staying ahead of potential equipment failures, manufacturers can maintain consistent production flow and protect their bottom line.
"An ounce of prevention is worth a pound of cure."
Understanding and effectively utilizing these core modules allows manufacturers to weave SAP's comprehensive tools into their operational tapestry. When these elements come together, organizations gain a competitive edge in the dynamic realm of modern manufacturing. The synergy of these modules enhances workflow, supports data-driven decision-making, and ultimately leads to an agile and responsive manufacturing environment.
The Integration of SAP in Manufacturing Environments
Integrating SAP systems into manufacturing environments is not just about technology; it’s about transforming how organizations operate at core levels. The importance of this integration cannot be overstated as it drives efficiency, reduces waste, and ultimately enhances capability to deliver on customer demands. Companies that successfully combine their operational processes with SAP frameworks often reap a myriad of benefits, such as streamlined workflows, improved transparency, and increased responsiveness to market changes. The challenge, however, lies in navigating the process of interfacing SAP with existing systems, sharing real-time data effectively, and fostering collaboration amongst departments.
Interfacing with Existing Systems
Interfacing SAP with pre-existing systems requires both strategic planning and technical finesse. Many manufacturers have legacy systems that crisscross their operations, from inventory management to production scheduling. Simply uprooting these systems can lead to alarm bells ringing across the organization. Instead, a more effective path involves adopting middleware solutions or APIs that allow seamless communication between SAP and legacy systems. For example, if a company uses a certain software for quality control, developing APIs helps bridge the gap, allowing SAP to pull relevant data and update inventory levels promptly. This not only keeps existing operations running smoothly but also enhances the efficiency of the new SAP system.
Key considerations for this interfaz include:
- Assessing system compatibility
- Ensuring data integrity during transfer
- Training employees on new workflows
- Choosing the right tools to facilitate integration
Real-Time Data Sharing
One of the standout features of SAP lies in its ability to provide real-time data sharing. In a manufacturing setup, time is often of the essence. For instance, a delay in accessing production metrics can thwart decision-making processes. By integrating real-time data sharing, companies can monitor production lines, track inventory levels, and forecast demand accurately without any lag. Achieving this seamless flow of information enables manufacturers to respond quickly to any operational hiccups.
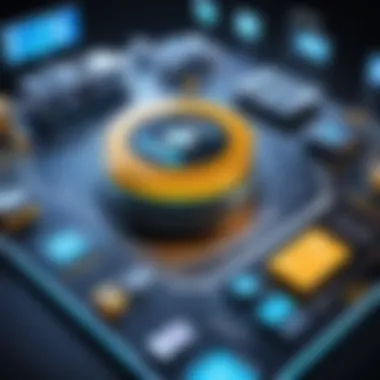
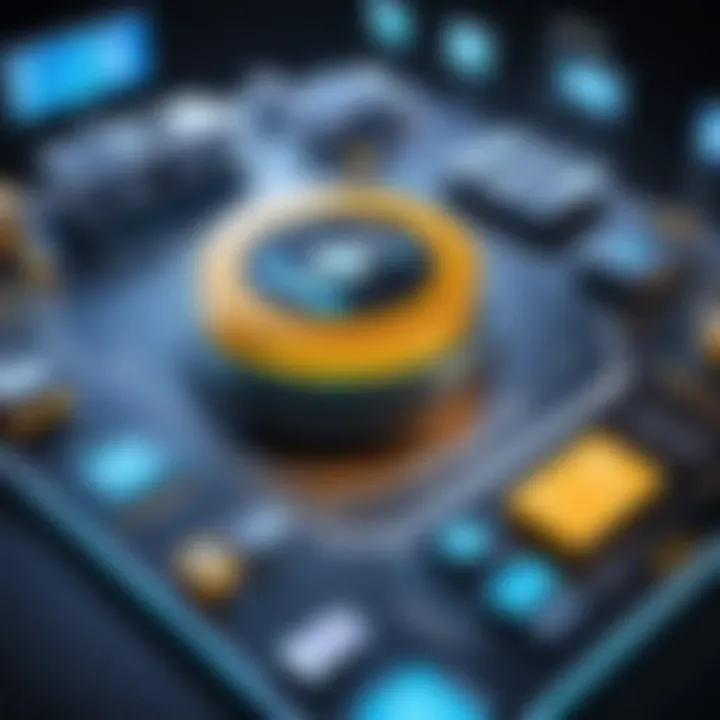
Using tools like SAP HANA, real-time analysis allows businesses to evaluate processes on-the-go, leading to timely adjustments and increased overall productivity. Not only does this create a more agile environment, but it also allows teams to make data-driven decisions to optimize resource allocation effectively.
Collaboration Across Departments
Collaboration is essential for any organization, and in the realm of manufacturing, SAP encourages the breaking down of silos between departments. Whether it’s production, logistics, or sales, having a unified platform can greatly enhance coordination. For instance, when production schedules are directly linked to sales forecasts via SAP, it allows companies to align their supply chain processes more effectively.
Effective collaboration can bring about:
- Reduced lead times on orders
- Improved quality control through shared insights
- Enhanced customer satisfaction due to better service delivery
The axiom "A chain is only as strong as its weakest link" resonates here; ensuring smooth collaboration paves the way for robust operational frameworks that can handle challenges head-on.
By fostering an environment where information flows freely, SAP promotes a culture of collaboration that can transcend departmental boundaries. A cohesive strategy encourages teams to work together to solve problems, harnessing collective intelligence to foster innovation and agility.
Benefits of SAP Implementation in Manufacturing
Implementing SAP in manufacturing is like equipping an organization with a Swiss army knife—packed with tools that help tackle various challenges in a seamless fashion. As the manufacturing landscape evolves, the need for effective solutions that drive efficiency, reduce costs, and bolster decision-making becomes paramount. This section examines these multifaceted benefits that SAP brings to the table for manufacturers, ensuring they stay competitive in a rapidly changing environment.
Enhanced Operational Efficiency
Operational efficiency is the wine that manufacturers crave in their daily operations. When SAP systems are integrated into manufacturing processes, they provide a solid framework for optimizing workflows. This system identifies bottlenecks in production, helping companies streamline processes and reduce waste.
- Automation of Routine Tasks: SAP automates many routine administrative tasks. Think about it—when materials are ordered automatically based on real-time inventory levels, workers can focus on processes that add real value.
- Standardized Processes: Using SAP, organizations can standardize procedures across all departments. This reduces errors and improves coordination. In factories that produce various products, having a standardized system becomes crucial.
- Real-Time Monitoring: Operational efficiency benefits significantly from real-time monitoring. For instance, a manufacturer can monitor machine performance, track output, and adjust orders on-the-fly, leading to substantial productivity gains.
In short, enhanced operational efficiency through SAP not only improves productivity but also contributes to a culture of continuous improvement, which is crucial for long-term success in manufacturing.
Cost Reduction Strategies
Cost reduction in manufacturing isn’t just about trimming fat—it’s about working smarter, not harder. With the integration of SAP, manufacturers can implement strategies that lead to significant cost savings, addressing both direct and indirect costs.
- Inventory Optimization: SAP helps manage inventory levels in a more controlled way. By optimizing stock levels, businesses can reduce holding costs. Too much stock ties up cash flow while too little can lead to production delays.
- Waste Reduction: The data analytics capabilities of SAP reduce waste by identifying inefficiencies in production. Manufacturers get insights into areas where materials are overused or processes are inefficient. Making adjustments here can lead to remarkable savings.
- Improved Supplier Relationships: SAP’s module for supplier management enables companies to negotiate better terms and prices with suppliers. By leveraging data, manufacturers can see spending patterns and adjust their procurement strategies to save money.
These cost-saving strategies make a compelling case for SAP adoption, as the investment in such systems can often be recouped through the savings they generate.
Improved Decision-Making Processes
In manufacturing, decision-making can often feel like navigating a ship through dense fog—without reliable data, steering in the right direction becomes a challenge. SAP transforms this landscape by providing comprehensive insights that empower decision-makers at all levels.
- Data-Driven Insights: With real-time data provided by SAP systems, executives can make informed decisions based on accurate information. Instead of guesswork, strategies are developed upon factual bases, leading to smarter business outcomes.
- Scenario Planning: SAP facilitates robust scenario planning, allowing manufacturers to evaluate various business scenarios and their potential impacts. This is essential in a volatile market—being able to predict the outcome of different strategies can be a game-changer.
- Cross-department Collaboration: When all departments operate from a centralized system like SAP, communication improves. Sales, production, and supply chain units can work collaboratively—reducing the risk of misaligned goals and fostering a unified organizational vision.
"In today’s manufacturing world, informed decisions are the oil that keeps the engine running smoothly."
Overall, the benefits of SAP implementation in manufacturing extend beyond mere operational gains. They shape the very way businesses strategize and execute their vision.
Challenges in SAP Adoption for Manufacturers
Adopting SAP systems in manufacturing is no small feat; it comes with a unique set of challenges that organizations must navigate to fully leverage the benefits of these systems. Properly understanding and addressing these challenges can mean the difference between a successful implementation and a costly failure. Manufacturers often face hurdles that can impede the efficiency, adaptability, and overall performance of their operations. Recognizing these obstacles is crucial not only for project managers and IT professionals but also for organizational leaders who aim to harness SAP's capabilities effectively.
User Resistance and Change Management
One of the most significant challenges that arise during the SAP adoption process is user resistance. Change, especially in well-established manufacturing environments, can be as welcome as a skunk at a garden party. Employees often feel a sense of discomfort when faced with new technology and workflows, which can lead to reluctance in using the new system. Their familiarity with existing processes makes it hard to embrace the unfamiliar.
Effective change management strategies play a pivotal role in overcoming this resistance. It is vital to communicate the underlying reasons for the SAP implementation clearly and continuously engage employees in the process. For instance, conducting workshops or training sessions that emphasize how SAP can streamline their day-to-day tasks can bolster acceptance. By framing the SAP system not just as a tool, but as a facilitator of improved work conditions, organizations can mitigate the fears surrounding the transition.
"The biggest obstacle to adopting new technology is the human element. People need to understand how it will help them, not just the business."
Cost and Resource Allocation
Financial considerations can be a double-edged sword in the context of SAP implementation. The initial investment can knock the wind out of many manufacturing firms' sails. There are direct costs associated with purchasing software licenses, hardware upgrades, and hiring consultants for seamless integration. Additionally, indirect costs—like potential downtime during the transition—can adversely affect production schedules.
To effectively address these financial factors, manufacturers should conduct a thorough cost-benefit analysis to uncover not just the upfront costs, but also long-term gains. Understanding that initial expenditure may yield increased efficiency and reduced operational costs down the line can help justify these investments. Furthermore, organizations should strategize resource allocation with foresight, prioritizing areas that would most benefit from SAP enhancements to get a grip on costs and ensure optimal use of available resources.
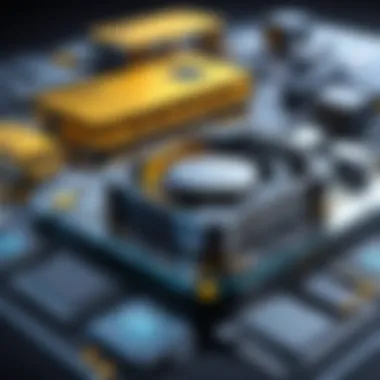
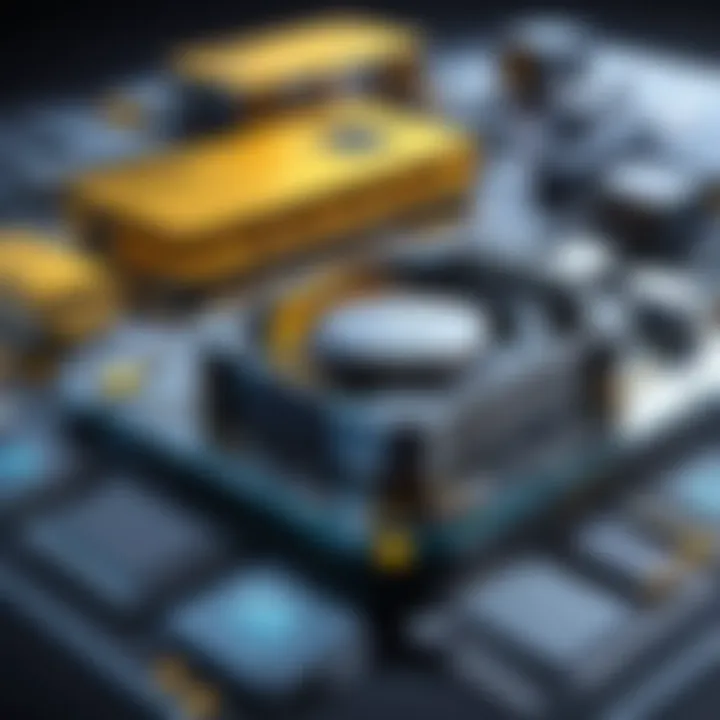
Skill Gaps and Training Needs
The implementation of SAP in manufacturing also unveils skill gaps within the workforce. Many employees may find it daunting to navigate the complexities of a sophisticated ERP system if they haven’t had previous exposure. A company’s internal talent pool is its richest asset, but if they lack the necessary skills to utilize the new system, this asset quickly becomes a liability.
Tackling this challenge requires a robust training program is indispensable. Finding the right balance between on-the-job training and formal education will be crucial. For instance, using simulators that mirror the SAP environment can provide hands-on experience without the risks associated with real-time operations. Also, involving employees in the customization of the SAP system can create a sense of ownership, enhancing their confidence and competence.
In summary, while challenges in the adoption of SAP systems are real and can be daunting, understanding and addressing user resistance, managing costs effectively, and training employees will position manufacturers to reap the full benefits of their investment. As organizations evolve along this journey, it becomes necessary to regularly revisit these challenges and adjust approaches to ensure a smooth transition into the SAP ecosystem.
Case Studies: SAP in Action within Manufacturing
The discussion of the role of SAP in modern manufacturing is enriched significantly through the lens of case studies. These real-world instances provide valuable insight into how various organizations leverage SAP systems to streamline their operations and address specific challenges. Case studies offer a visual representation of theoretical concepts, turning abstract ideas into tangible outcomes. This section will unpack two critical components of case studies in SAP manufacturing: success stories and lessons learned.
Success Stories
Success stories of SAP implementation present compelling narratives that underscore the capabilities of these systems in manufacturing processes. One notable example is that of Siemens, a global leader in automation and digitalization. Siemens embraced SAP's Enterprise Resource Planning (ERP) solutions to enhance productivity across its sprawling manufacturing facilities. By integrating real-time data with SAP modules, Siemens improved inventory visibility and reduced production errors, achieving higher throughput. This transition not only fostered operational efficiency but also significantly cut costs associated with lost materials and labor inefficiencies.
Another success story comes from Boeing, who integrates SAP to manage parts of its complex supply chain. The aerospace giant utilized SAP to enhance collaboration with suppliers and optimize logistics processes. The centralized platform enabled Boeing to respond swiftly to demand fluctuations and coordinate with its manufacturing partners globally. The results were clear: enhanced production timelines and improved quality assurance, showcasing SAP's potential in high-stakes environments.
These examples illuminate how specific organizations adapted SAP to solve unique challenges while drawing parallels and lessons applicable to various other manufacturers.
Lessons Learned
While the success stories paint a picture of triumph, the lessons learned through these implementations are equally vital. A crucial takeaway from the SAP experience is the importance of change management. Many manufacturers underestimate resistance from users when introducing new systems. Effective engagement strategies from the beginning can ease the transition process. For instance, companies like Nestlé invested heavily in user training sessions. They discovered that informed employees exhibit greater acceptance of technological shifts, leading to smoother integration phases.
Moreover, a prevalent issue uncovered is that not all SAP solutions are a one-size-fits-all approach. Different sectors within manufacturing may necessitate tailored applications. An organization like Coca-Cola, with its vast distribution network, faced hurdles with capacity planning. They learned through rigorously assessing their options that customizing certain SAP modules specifically for their operational style was key to overcoming logistical challenges.
"Not every manufacturing scenario is alike; customization of SAP systems to meet individual needs is paramount for success."
In navigating these lessons, firms can better prepare for the journey of SAP adoption.
Future Trends in SAP and Manufacturing
As technology steadily evolves, the role of SAP in manufacturing is shifting, setting the stage for new advancements and trends. Recognizing these movements is crucial for businesses aiming for competitive edge. By staying abreast of future trends, manufacturers can align their operational strategies, ensuring they maximize efficiency, productivity, and sustainability. This section delves into two pivotal elements shaping the interplay between SAP systems and the manufacturing sector: the integration of artificial intelligence and the growing focus on sustainable practices.
The Role of Artificial Intelligence
Artificial intelligence, often referred to as AI, is emerging as a game changer in the manufacturing landscape. Organizations are beginning to grasp the power of AI, which can analyze vast amounts of data far quicker than any human could. In conjunction with SAP systems, AI can foster predictive analytics that help in forecasting demand, optimizing inventory, and even fine-tuning production schedules.
- Predictive Maintenance: SAP's integration with AI allows for predictive maintenance – a proactive approach to machine upkeep. This means instead of waiting for a machine to fail, companies can anticipate breakdowns before they happen. Sensors gather real-time data on machine performance, and AI processes this information to predict potential issues. As a result, the downtime gets minimized, helping companies save both time and resources.
- Enhanced Decision Making: Data-driven decision-making becomes much more robust with AI. Utilizing historical and real-time data, SAP systems can provide actionable insights tailored to specific operational needs. This advancement allows managers and teams to make informed decisions rather than relying on intuition alone.
- Customized Production: The rise of mass customization, facilitated by AI integrated within SAP, poses fresh opportunities. Manufacturers can utilize data to tailor products based on buyer preferences while maintaining efficient production processes. In this way, AI turns traditional manufacturing on its head, pushing toward more personalized outputs.
"AI is not just a tool; it’s a partner in innovation for modern manufacturing."
Sustainability and SAP Solutions
In today’s increasingly eco-conscious world, sustainability is not just a buzzword but a necessity for the manufacturing sector. SAP solutions are evolving to prioritize sustainability, enabling organizations to implement greener practices. Businesses that leverage these tools are not only contributing positively to the environment but are also reaping economic rewards.
- Resource Efficiency: SAP systems can enhance resource management by closely monitoring material usage and energy consumption. With the ability to analyze workflows and identify waste, organizations can optimize their processes, which ultimately leads to less environmental impact and reduced costs.
- Regulatory Compliance: As regulations on sustainability become stricter, SAP can assist companies in ensuring compliance. By maintaining transparent and accurate records of sustainability efforts, manufacturers can avoid potential penalties and foster corporate responsibility.
- Circular Economy: SAP promotes principles that support a circular economy approach, where waste is reduced, and products are reused or recycled. Leveraging SAP, organizations can track product life cycles, enabling them to develop strategies that align with sustainable manufacturing goals.
In essence, the future of SAP in manufacturing is bright, intertwined with avenues that encourage both technological advancements and sustainable practices. Agile systems that adapt to these trends will lead the way in creating a more efficient, responsible, and innovative manufacturing landscape.
Finale
In the ever-evolving landscape of modern manufacturing, the role of SAP systems cannot be overstated. Their integration into manufacturing processes has become a linchpin for operational excellence, reflecting not only an increased capacity for efficiency but also a strategic edge in decision-making. As manufacturers strive for heightened productivity and streamlined operations, understanding the intricate workings of SAP emerges as a key factor.
Summary of Key Insights
The exploration of SAP within manufacturing has illuminated several vital points:
- Operational Efficiency: SAP systems enhance productivity by enabling seamless communication between various business departments, ensuring that everyone from production to sales is on the same page.
- Cost Management: Implementing SAP can reduce operational costs through optimized resource allocation and waste reduction.
- Real-Time Data Access: The ability to access and analyze data in real-time allows for quick adaptations to market changes, boosting overall responsiveness.
- Training and System Integration: There's a need for comprehensive training programs to alleviate user resistance and ensure that employees are well-equipped to utilize SAP tools effectively.
The interconnectedness of SAP systems promotes a culture of continuous improvement, essential for manufacturers aiming to stay competitive.
The Path Forward for Manufacturers
As manufacturers look ahead, several considerations are crucial for leveraging SAP technology effectively:
- Investing in Training: It’s paramount that companies invest in thorough training for employees. Familiarity with SAP not only minimizes resistance but also maximizes the return on investment.
- Continuous Innovation: Staying updated with the latest SAP advancements will ensure that manufacturers are not left behind. This involves periodic training and system upgrades.
- Flexibility and Scalability: Manufacturers should adopt flexible and scalable SAP solutions that grow in tandem with organizational needs.
- Sustainability Initiatives: As sustainability gains priority, integrating green practices within the SAP framework will not only enhance corporate responsibility but may also open doors to new markets and customer bases.
In summary, tapping into the full spectrum of SAP capabilities is not just a matter of enhancing existing processes; it’s about future-proofing the organization against rapidly changing manufacturing dynamics. With a proactive approach towards integration, training, and sustainability, manufacturers can effectively harness the power of SAP to drive their growth in the years to come.